Article and pictures by Alex Varv
Foreword: This article was first published in Aero Connections Magazine.Later, it was published on www.poweredparaglider.com where it was lost.The www.aerocorsair.com Inventions Page had only a link to this article.Thanks to a few pilots who saved my article, I could recover it, review, update and re-publish it here on this page.
This article has been translated into many languages around the world and helped many pilots to run their engines correctly thus increasing power, preventing overheating and reducing engine maintenance.
In order to operate properly, any internal combustion engine needs an optimal mixture of fuel and air. This is achieved by means of a device that will atomize the fuel and mix it with air to a very precise mixture ratio.
There are two main types of carburetors:
a) the float type carburetor, also known as the bowl type
b) the membrane type, also called the diaphragm carburetor.
c)fuel injection with TBO throttle Body and direct injection when the fuel is injected directly into the combustion chamber or venturi (Aero Cors-Air USA LLC already has a fully functioning TBO system sold for the time being, exclusively to military contractors)
Since most paramotors are equipped with the membrane type carburetor (be it a Walbro, Mikuni, or Tillotson), in this article, I will discuss the tuning of the Walbro because it is the most commonly used in the industry.
Before getting deeper into the tuning, we shall analyze the difference between the float type and the membrane type carburetors and point out their advantages and disadvantages. Of course, in order to achieve the best possible mixture, the ideal carburetor would be a throttle body injector, monitored by a computer like the systems used in modern cars. Aero CityplaceCors-Air country-regionUSA uses such a system on the Cors-Air M25Y Black Devil engine (electric start version)
For the time being, the membrane carburetor is the most commonly seen in the paramotor world.
The advantages of the diaphragm carburetor over the "good old Bing" are as follows:
a) they can be mounted in virtually any position
b) they are much lighter, cheaper, and have a self contained vacuum powered fuel pump
With all these good properties versus the float type carburetor, the membrane type has a more peculiar feature. It is more difficult to tune that is, if one is not familiar with it.
From my knowledge and experience, I must say that there are no two people alike. The is also true with engines. From many telephone calls from my readers, after this article had been published in Aero Connections Magazine, I would like to point out that ALL carburetor settings, even those given by the manufacturers, are approximate. This is why I experimented with my engine and carburetor. This article takes the reader, step by step, through the tuning process and if done properly, the engine itself will TELL the pilot what the proper settings are.
This article, over the years has been translated to many languages including Japanese.
For a proper and safe combustion, any engine needs to be delivered a relatively precise mixture of air and atomized fuel, over a wide range of operating conditions and RPMs. The operation can be from idle, usually 2,000 to 2,300 RPMs, to full power,(usually from 6000 to 6,500 RPMs if not even more) depending on the engine, reduction, propeller size and type.
The ideal air to fuel mixture ratio is anywhere from 12:1 to 16:1 (example 16 volumes of air and one volume of fuel) and it depends on elevation, type of fuel, oil to fuel mixture, ambient temperature and engine.
The membrane carburetor has four adjustments:
1) The fuel metering system (needle valve) located underneath the membrane,
2) The idle screw,
3) The high RPM adjustment screw
4) The low RPM adjustment screw
Most two stroke paramotor engines have an average TBO (time between overhaul) from 300 to 500 hours but many of them run much shorter. It is mainly because of improper carburetor tuning. I find many pilots, due to lack of training and knowledge, do not pay much attention while tuning their carburetor. Some of the engine manufacturers, in their engine owner's manuals, do not even bother to describe how to tune a carburetor at all!
I spent almost two years experimenting and I can tell that it cost me many parts, frustration and headaches, but in the end, it was well worth it.
After all these being said, we can now proceed in analyzing the types of air/fuel mixtures. Please, do not get confused with oil/fuel mixtures versus air/fuel mixture. In the following, we will analyze the air/fuel mixture.
The Lean Mixture
The lean mixture occurs when the fuel is burned in too much air. This mixture gives maximum power or not enough power, depending on how lean the mixture is. With a lean mixture, higher than normal engine operating temperatures occur thus creating less carbon deposits. The engine runs cleaner but hotter and smoother with no smoke.
WARNING, overheating is very likely to occur. In this situation, the temperature above the piston can rise almost instantly and can burn the piston, rings, cylinder and even cylinder head. Overheating cannot be detected soon enough with a cylinder head temperature gauge. By the time the temperature reaches the probe mounted underneath the spark plug, the piston will have already suffered damage, seized or burned. Only an EGT (exhaust gas temperature) sensor mounted or inserted directly into the exhaust manifold can detect this temperature almost instantly.
Usually, a very "lean engine" will "blow" in a matter of seconds. Therefore, when tuning your carburetor: when a drop in RPM occurs while leaning the mixture, the carburetor MUST be tuned immediately to the rich side! A common symptom of a lean mixture will be backfiring, when the engine is turned off.
NOTE: The spark plug color of the ceramic and electrodes will be white or light gray.
The Rich Mixture
The rich mixture is the opposite of the lean mixture. In this case there is too much fuel burning in not enough air (Oxygen) The burn is incomplete, slower, the engine smokes, runs rough, does not deliver full power and the burn leaves a lot of carbon residue. Other dangers with a too rich mixture are: a longer take off run (the engine lacks power), poor climbing, and the engine may all together quit in flight because the spark plug gap may become "shorted" by carbon deposits or even carbon particles. At the same time, the rapid carbon build-up can cause pre-ignition and cylinder wall scoring. This will reduce the compression of your engine. The carbon deposits will plug the decompression hole in the cylinder (if your engine has an internal decompressing orifice)
Besides checking the spark plug color, carbon build-up can be suspected if the compression seems higher than normal (detected by the starter rope needing to be pulled harder than usually)
Note: (spark plug color) the ceramic and the electrodes will be very dark brown or black and heavy carbon deposits may be visible.
The Safe Mixture
The normal mixture is a compromise between the lean and the rich mixture, but slightly on the rich side. This state will decrease the engine performance somewhat (usually about 80-100 RPMs below the peak). In this case, the almost optimal amount of fuel is burned but in less air than in the case of the lean state. The mixture is slightly rich. We get slightly less performance than in the lean state but the engine will not overheat, will be safe, will shake less, if at all, and the carbon build-up will be at an acceptable rate.
NOTE: (spark plug color) the ceramic and the electrodes will be medium brown to dark brown. No carbon deposits should be seen.
All these adjustments will be much easier if a Lambda meter is used. This device measures the CO and CO2 concentrations in the exhaust gases and will show how rich or lean the mixture is.
However such a device is expensive ($250.00)
Using my above recommendations will allow the pilot to tune the carburetor without such a Lambda device.
For an easy and precise tuning, we must have a good access and maximum comfort, while adjusting the IDLE, LO and HI screws. On all WALBRO carburetors, only the HI screw has a comfortable handle that allows it to be turned, while the engine is running.
Note: all adjustments should be done on a running engine. When turning the IDLE or LO with a screwdriver, the screwdriver is usually "knocked off" by the screw because of the vibrations, and this operation becomes a nightmare. It is not very difficult at all to have the screwdriver slip through our fingers and fall or even be caught by a rotating propeller at 2,000 or more RPM.
Having all these in mind, I improved my WALBRO: (see picture) I soldered an "L" shaped nail into the groove on the head of the screw. Prior to soldering, the end of the nail was flattened with a hammer, to give it a "screwdriver shape", slightly thinner than the groove (slot) itself. The gap was filled with soldering compound, and I also added more compound above the head, in a conical shape around the nail.
We have a special DVD that illustrates this and also shows how to overhaul a membrane carburetor. Additionaly the DVD explains how to adjust the ideal "pop-off" pressure in the carburetor.
The picture above shows that the Idle Screw, instead of an “L” shaped nail handle received a flexible braided steel cable which allows the operator to have an easier access to it especially if the carburetor is equipped with an air-box instead of a classic air filter.
This improvement helps enormously to perform all the tuning with two fingers, and with the engine running all the time. This is a safe and easy way to tune. If the soldering is thick enough, vibrations will not break it. I have been using my "remanufactured screws" for years with excellent results. The tuning is very easy and extremely accurate. This improvement can be certainly done on other membrane carburetors as well. There is another thing I did; I installed my TINY-TACH on the throttle (see picture below) and when adding power with one hand, I can see the RPMs and do the tuning with the other. There are other advantages as well. While airborne, we know how much power we have and this is important. For example, if we notice an unusual increase in RPMs, say instead of 6,200 we notice 6,400 at full power, we can suspect a slipping reduction belt. Before it breaks or burns, we can land safely, still having a "running prop"! On the other hand, if we climb and notice a slow but continuous drop in RPMs (above 2000 - 3000 ft MSL) and this happens when we attempt to thermal on a "bad day", we know immediately that the mixture is becoming rich. The advantage of a TINY-TACH mounted on the throttle handle, is therefore a much better solution.
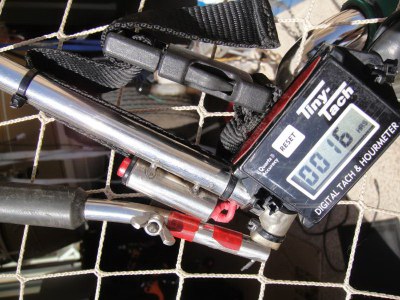
After so much "theory" we can start the tuning process.....
Carburetor Tuning
Before we attempt to turn any adjustment screw on our Walbro , Tillotson, Mikuni or other diaphragm carburetor, we should check the following:
1) Fuel: the gas and oil mixture must be fresh, less than 72 hours old. The reason for this is because if the fuel mixture is kept longer than 72 hours, the properties of the fuel mixture will be altered.
2) Fuel tank vent: open.
3) Air filter: clean.
4) Fuel lines: sound with all connections tight, including the primer bulb if present
In addition, please make sure that none of the following applies to your engine: leaky crankcase gasket and crankshaft seals, broken or leaky carburetor gaskets, vacuum hose or damaged reed valves (if the engine is equipped with them) These items can cause a rough idle and lean mixture that may not be possible to eliminate while tuning the carburetor.
The entire fuel line and fuel filter must be filled with fuel, with no air bubbles, which can also cause a lean mixture or even engine failure. The best way to eliminate the air bubbles is to squeeze the priming bulb while pushing the membrane down. This way the needle valve will open and the air will be pumped out from the line. To prevent engine flooding, the paramotor should be tilted towards the carburetor side to allow the excess fuel to drain. However, if the engine becomes flooded in this stage (will not start), here is a trick that works with no need to remove the spark plug. Turn off the main switch to prevent an accidental start of the engine. Fully open the throttle and hold it open while tuning the prop 3 to 4 full revolutions in the opposite direction of its normal rotation. If the flooding was not too serious, the engine will start. If it does not, the spark plug must be removed and with a few pulls of the recoil starter or electric (if existing) the engine will be cleared. After these checks you can proceed with the tuning.
Important note: the above method will NOT work if we have a flooded inverted engine. If this were the case, the flooding will give us a very clear symptom: the compression of the engine is increased.
This is caused by the fuel accumulation in the combustion chamber and because the fuel is below the exhaust port, it will be impossible to clear it. The only remedy is to remove the spark plug.
Considering that the metering system (not discussed in this article) is properly set, I must stress that very often, even at the same field the carburetor should be tuned because the density altitude or in other words the atmospheric pressure changes. If the pressure increases, the air becomes denser and because there is more oxygen in it a lean mixture will occur if the previous carburetor tuning was performed before the atmospheric pressure increased. Conversely, if the pressure dropped, our mixture will become rich. Also, if we climb to higher altitudes the mixture will become richer and richer, and as we climb above approximately 3,000 ft the fuel mixture will be too rich. For this type of flight I strongly recommend a remote mixture adjustment system that is available on the market or better, it is described on The Inventions Page.
The engine must be "warmed up" or in other words brought to operating temperature before tuning the carburetor. I suggest the use of at least a cylinder head temperature gauge and a "Tiny Tach" to monitor the RPM as well. Look in your owner's manual or contact your paramotor manufacturer for your engines normal operating temperature.
NOTE: During warm up or immediately after starting the engine (cold engine) and even if the engine was tuned before, the mixture will be lean. This is normal since the lower temperature of the carburetor, crankcase, piston, and cylinder will create a less volatile environment that causes the fuel not to evaporate as easily as in a hot engine. Thus, even with a correct carburetor tuning for the existing air pressure, the engine will not accelerate and will shake.
At this stage we can turn the LO mixture screw counter clockwise, usually 1/8 of a turn from its existing setting. This operation will increase the idle RPM, since the mixture becomes richer and the engine will run smoother. However, engines such as the Solo 210, will run rough and even vibrate. A slight increase in fuel flow will eliminate the vibrations which are unnecessary and can stress the cage and engine mounts.
There is no need to depress the throttle yet.
As the engine warms up the idle RPM will obviously drop since the mixture becomes too rich. Conversely, we should slightly close the LO mixture screw to its primary position (position of the low mixture screw before starting the engine)
Entry positions of the HI and LO screws for:
Simonini :
LO minimum: 1/8 - 1/4 of a turn from fully closed.
LO Maximum 1/3 of a turn from fully closed
HI screw minimum 3/4- 1 turn from fully closed
Maximum 1 3/4 from fully closed or more (if you follow my recommendations, the engine itself will tell how much you need to open the LO and HI screws)
DK GT:
LO screw one turn from fully closed
HI screw one full turn from fully closed
Any adjustments should be done for both 1/8 of a turn to the left (rich side) or right (lean side)
Cors-Air M21Y, Cors-Air M25YBlack Devil:
LO screw ¾ of a turn from fully closed
HI 1 and ¼ to 1 3/4 of turn from fully closed
Black Magic:
LO screw ½ from fully closed
HI 1 to 1 1/2 turn from fully closed
For other engines, please check your owner's manual!
It is important that the entry settings are correct.
NOTE: If the above settings are not enough to properly tune the engine, that is, you need to open the screws past the maximum setting, you may have a partially clogged carburetor, a leaky reed valve or an air-leak in the crankcase or carburetor gasket.
When the idling temperature has reached approximately 200 degrees you can continue with the tuning of your carburetor. With the LO and HI screws set at their entry settings, it is time to set the idle RPM. In this stage, a tachometer becomes very handy. The idle speed. for a 45 inch propeller will be around 2,250 RPM while for a 48 inch propeller it will be around 2,000 - 2,100 RPM.
If we do not know the manufacturer's specs, it is very easy to establish the optimum Idle RPM on our engine.
A too high Idle will generate too much thrust . A too low RPM can cause stalling or rough idle. It is always safer to set a higher idle RPM, since while descending with a low idle the engine can "load-up" and stop!
Once the idle RPM has been set, we should proceed with the LO screw setting.
Depressing the throttle slightly we listen to the engine. If the engine hesitates to accelerate, the LO screw should be opened 1/8 of a turn. If we open the screw too much, the engine will not accelerate smoothly and start shaking (too rich of a mixture). In this case we should close the LO screw slightly. We repeat this procedure until the engine reacts smoothly when adding power. Meanwhile, a readjustment of the idle speed may be needed.
After the LO mixture has been adjusted, we proceed with the HI screw adjustment. After securing the paramotor, we open the throttle to full power. We turn the HI screw to the left or right until the maximum RPM is reached. From this position just a slight turn to the right should cause a significant RPM drop. This means the lean side of the mixture has been achieved. Immediately we OPEN the screw to the left to prevent the engine from overheating!
Let us repeat once again this critical step:
At full power we tune for maximum RPM, then we close the HI screw more, until a drop in RPMs is noticed. When the drop in RPMs occurs we open the HI screw again until we reach maximum RPMs once again, and then we open the screw more until we have a drop of 20 to 60 RPMs. In this position the carburetor will be perfectly tuned slightly on the rich (safe) side.
Next, we should close the throttle and recheck the idle and the LO screw adjustment. If the carburetor was tuned properly, the idle will return to the normal setting described above. To put it in a nutshell, if the engine idles and accelerates smoothly, does not smoke and achieves 20- 60 RPM below maximum RPM, the carburetor is tuned correctly.
There is something to be said about "Four Cycling".
Some carburetors are prone to four cycling, which means that both HI and LO screws are partially active at the same time. This will not harm the engine but it will reduce power, and the engine will start shaking slightly. If the rough operation continues above 4,500 RPMs while adding power, the mixture is too rich. It is safer to adjust the LO screw (slightly close it) while holding the throttle in this range. If instead of the LO screw, we close the HI screw (for the same result), we will end up with a lean mixture on the high RPM side. Remember, even a slightly leaner mixture on the low RPM side is safer than on the high RPM side. Besides, a two-cycle engine should not be run too long on idle because the engine is less lubricated, the engine temperature is low and a carbon build up will occur faster, thus fouling the spark plug. If kept very long in this state, the engine may stop. Therefore, like with an airplane, when descending with idle RPM, it is advisable to open the throttle from time to time to "clean" the engine.
Engine Operation Temperatures
For the Solo 210, Hirth, Simonini, DK or Cors-Air engines, the normal operating idle RPM temperature is about 200-220 degrees Fahrenheit. The never exceed temperature is 482 degrees Fahrenheit, and caution here is strongly recommended since we are close to the seizing point of the engine.
With a properly tuned carburetor you will barely reach 360 to 380 degrees Fahrenheit at full power. Now it becomes obvious that having a cylinder head temperature gauge installed is a very good thing.
Also, Aero Cors-Air USA has introduced a specially designed cooling shroud for the cylinder head which dramatically lower the CHT temperature
Spark Plug Color
The color of the spark plug should be checked after every flight but a new spark plug needs about one hour to reach the real color. For example if you fly with a brand new spark plug for 15 minutes with a perfectly tuned carburetor, the color will seem too light. The earlier mentioned standard colors for the lean, rich and optimal air/fuel mixtures are only general rules. The color will be affected by other factors such as oil/fuel mixture ratio, type of fuel, fuel additives such as lead substitutes, octane boosters etc. Some oils with certain detergents will give a lighter color as well.
The color of the spark plug is also affected by the position of the spark plug in the cylinder head. For example in a Solo 210 the carburetor side of the plug will be much lighter than its exhaust port side. In a DK engine where the plug is centrally placed, the tan on the plug will be more uniform. Also if you use anti-seize compound on the threads of the plug, due to a more limited heat exchange between the spark plug may become hotter thus giving a lighter color.
After many months of experimenting, I must say, in conclusion, that a membrane type carburetor, if properly tuned, has some advantages over the float type.
We should always have in mind that with a perfectly tuned carburetor, the engine will last longer and above all we will fly safer.
Remember: Tune twice. Fly once!
Alex Varv
|